Beyond the Basics: Advanced Strategies for Australian Workplace Injury Prevention
Integrating Data, Technology, and Culture to Proactively Prevent Workplace Injuries
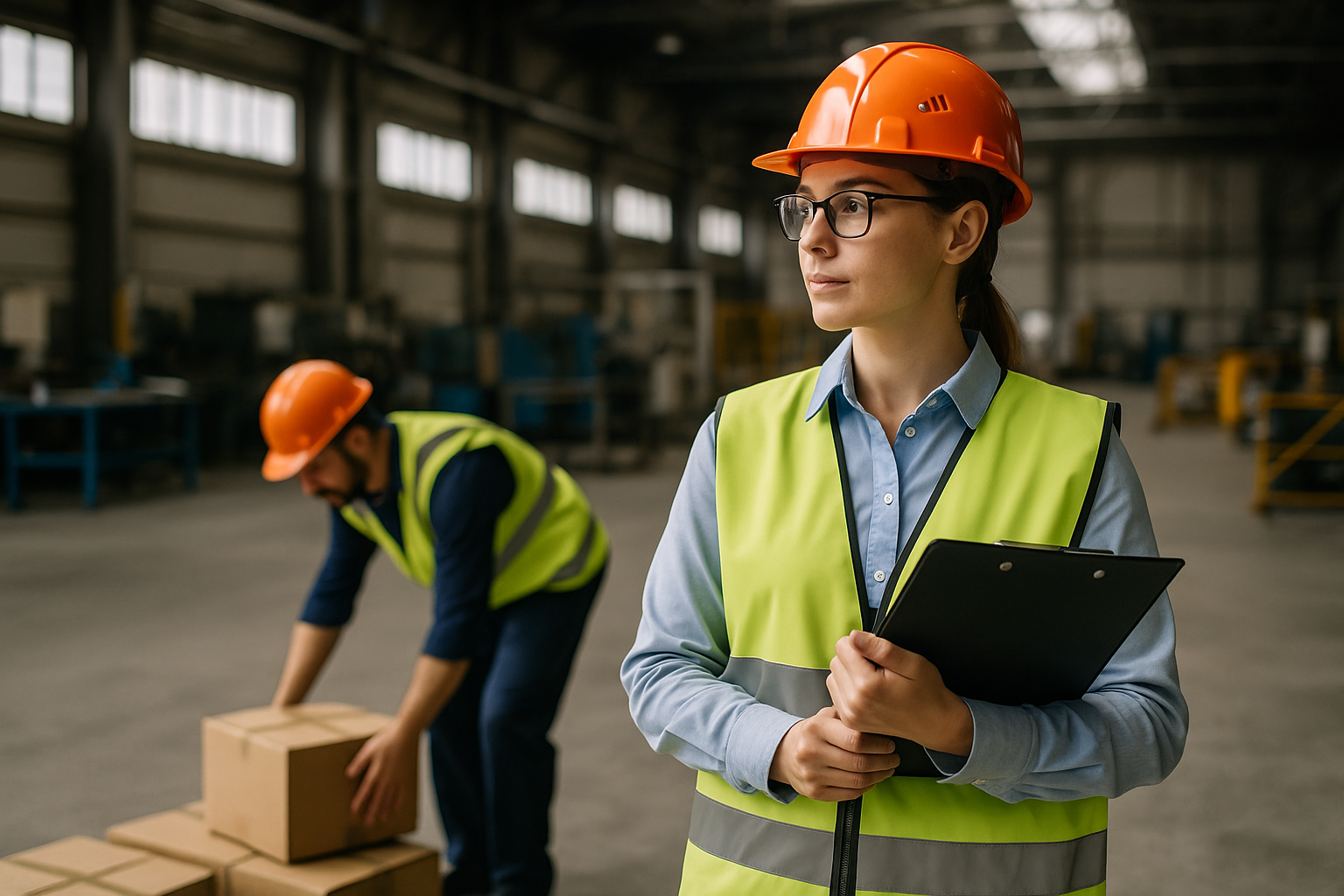
Basic workplace safety measures, whilst essential, are often insufficient in addressing the complex challenges of modern workplaces. To truly minimize injury rates and foster a culture of safety, Australian businesses must adopt advanced strategies that go beyond the basics and adopt a strategic approach. This means incorporating data-driven insights, predictive modelling, and leveraging cutting-edge technologies.
Moving Beyond Basic Safety Training
While mandatory safety training is crucial, it's often insufficient on its own. To create a culture of safety, employees need ongoing training and development focusing on risks at their root cause:
- Specific job hazard analysis: In-depth assessments of individual tasks and processes identify specific risks and vulnerabilities.
- Ergonomic evaluations: Analysing workstations and work processes to identify ergonomic risk factors, such as awkward postures and repetitive movements, which lead to MSDs (Musculoskeletal Disorders). Adopting technology and potentially wearables
- Linking employee wellbeing to safety: Proactive monitoring of employee health and wellbeing ensures you can understand trends in risk prior to an injury. You may choose to monitor fatigue levels, mood or live task risk levels. This includes physical and mental health factors. Early identification allows for support, correction and prevention of accidents and injury.
- Emergency response training: Moving beyond simple theoretical knowledge, providing regular practical training and drills for the most serious of emergencies, ensures employees are ready to respond effectively in real situations.
Leveraging Data and Predictive Modelling
Advanced injury prevention strategies harness the power of data. The key is to collect and understand data from lead sources AND lag sources. This involves:
- Collecting and analysing safety data: Tracking injury rates, identifying common causes, and using this information to pinpoint high-risk areas and target preventative measures. This could encompass recording near misses and using the data to predict where and when accidents are most likely to occur.
- Predictive modelling: Utilizing data analytics to forecast potential hazards and risks. Sophisticated algorithms can identify patterns and trends indicating potential problems.
- Implementing wearable technology: Using devices to monitor employee movements and physiological data, providing real-time warnings of potential risks such as fatigue, poor posture, or unsafe working conditions. Early warning signs allow for interventions before injuries occur. While there is an initial cost in purchasing and implementing the technology, the return on investment is usually substantial when considering the cost of workplace injuries.
Creating a Strong Safety Culture
Beyond technological advances, fostering a strong safety culture is paramount. At EMP Onsite, our safety leadership training identified key themes indicating poor safety culture. This included statements such as “my leader only talks to me when something is wrong” and “I never receive positive feedback” highlighting a lack of support and poor interpersonal relationships.
Many of these factors can be improved by;
- Promoting open communication: Employees feel comfortable reporting hazards and concerns without fear of retribution.
- Encouraging employee participation: Actively involving employees in safety planning and decision-making.
- Recognising and rewarding safe behaviour: Incentivising safe work practices to reinforce positive behaviours and encourage teamwork.
- Leading by example: Management demonstrating a strong commitment to safety, walking the walk, not just talking the talk.
Implementing Advanced Technologies. What are my options?
Technology is now an essential tool in your arsenal to analyse emerging risk trends. Examples include;
- AI-powered risk assessment tools: These tools analyse vast amounts of data to identify and prioritize hazards. New advances allow upload of photo or video to support incident reporting, non-compliance against regulations and even task analysis.
- Virtual reality (VR) training: Immersive VR simulations provide realistic training scenarios to better prepare employees for handling dangerous situations. There are a range of experiences available including occupational violence simulators, fire simulators and even emergency response simulation training.
- Wearable sensors: These sensors monitor workers’ biometrics and movements, analyse task risk and benchmark risk across your organisation, detecting early warning signs of potential injuries.
By integrating these advanced strategies into your injury prevention program, you can significantly reduce workplace injuries, minimizing both the direct and indirect costs and creating a safer, happier, more productive, and ultimately more profitable workplace.